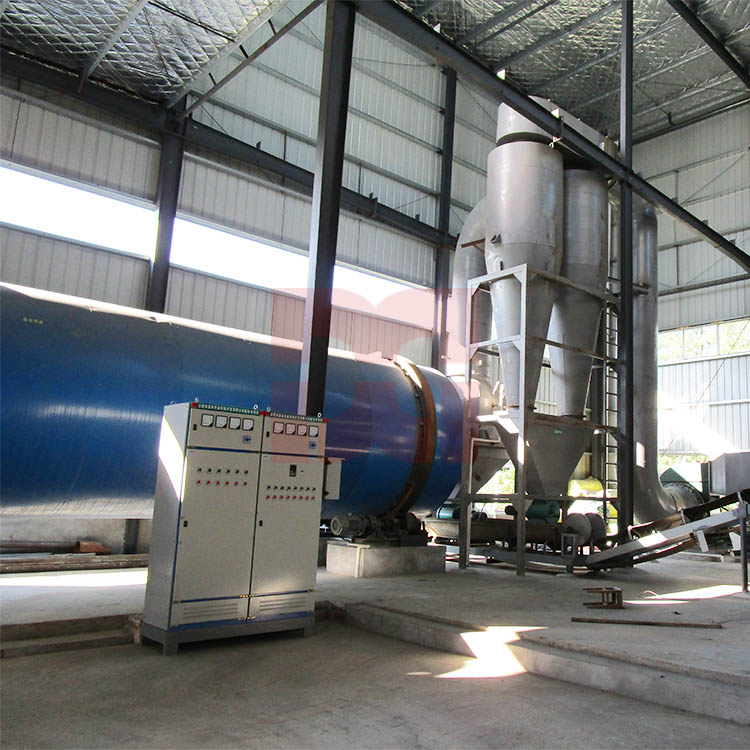
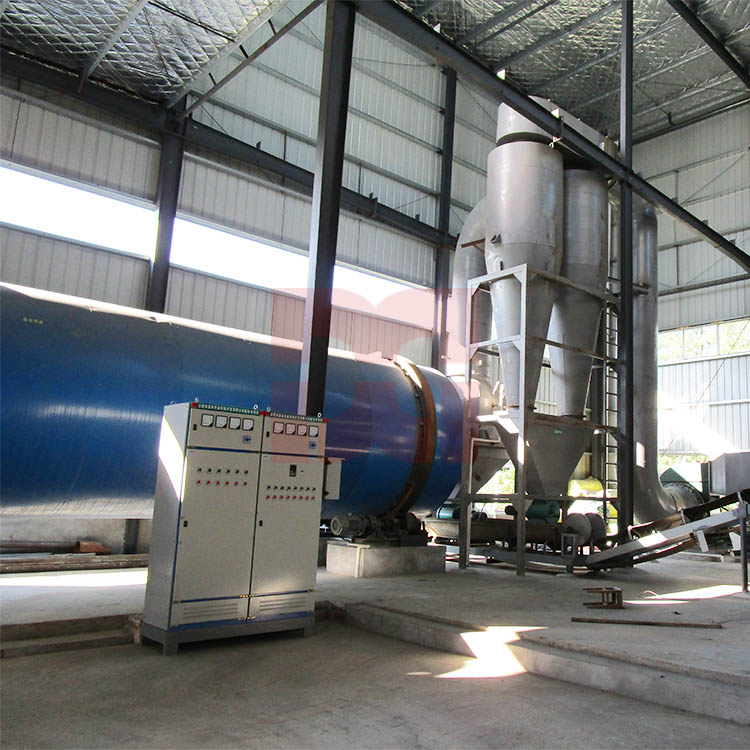
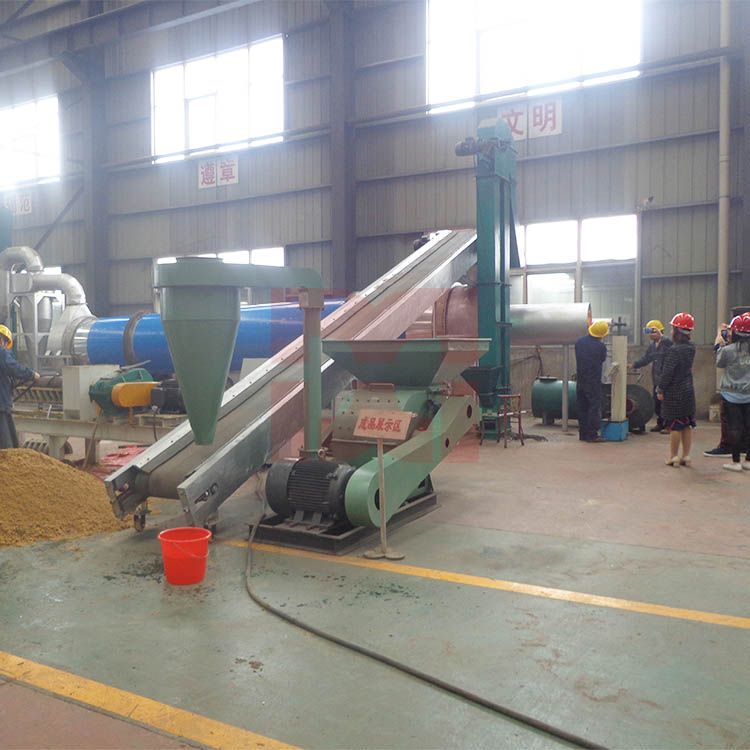
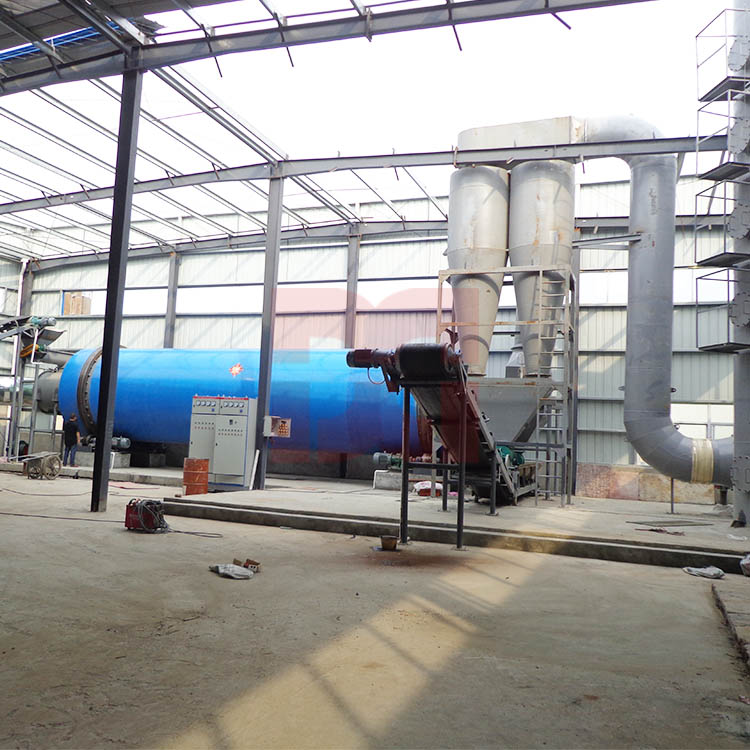
Biomass dryer is suitable for drying wood chips, sawdust, straw, coconut shreds, alfalfa, bagasse, pomace and other biomass fibers. And the final product can be used as biofuel, animal feed, etc.
Biomass Rotary Dryer Working Principle
Material enters the inner layer of the rotary drum by the feeder to realize downstream drying. Material is continuously picked up and scattered under the inner lifting board to realize heat exchange in a spiral manner. The material moves to the other end of the inner layer and enters the middle layer for countercurrent drying. Material is continuously raised in the middle layer and moves forward. The material in the middle layer fully absorbs the heat not only from the inner drum but also from the middle drum, at the same time prolongs the drying time, where the material reaches the expected drying state. The material travels to the other end of the middle layer and falls into the outer layer. The material travels in a rectangular multi-loop manner in the outer drum. The material that achieves the drying The effect is quickly discharged from the drum under the action of hot air.Wet material failing to achieve the drying effect cannot move quickly because of its own weight. Material is fully dried in this rectangular lifting board, so as to achieve the purpose of drying.
The Zhengzhou Dongding biomass dryer adopts a new three-cylinder structure. The cylinder is equipped with a lifting board and material guide plate with different angles and spacings. The special structure makes the inner cylinder and the middle cylinder surrounded by the outer cylinder form a self -insulation system. The heat loss of the cylinder is significantly reduced. The energy-saving three-cylinder dryer can make full use of waste heat, reduce heat loss, increase the exchange area, and greatly increase the evaporation intensity per unit volume of the dryer, thereby effectively increasing the heat utilization rate, reducing energy consumption, and can also meet the drying requirements of kinds biomass fiber.
Biomass Rotary Dryer Features
1. The drying strength is large. Because the material is highly dispersed in the airflow, all the surface of the particles is almost the effective drying area.
2. Large processing capacity and high thermal efficiency. When drying unbound water, the thermal efficiency can reach 80%.
3. The material feeding speed is controlled by frequency conversion speed regulation, which can easily adjust the required final moisture according to user needs.
4. The final product has low material temperature and high thermal efficiency, which is conducive to the long-term use of dust removal equipment and prolong the service life of dust removal equipment;
5. Adopting new energy-saving hot blast stove, which is thermally controllable, simple operation, and coal consumption reduced by about 60%;
6. Multiple heating sources available, such as coal, biofuel, etc.
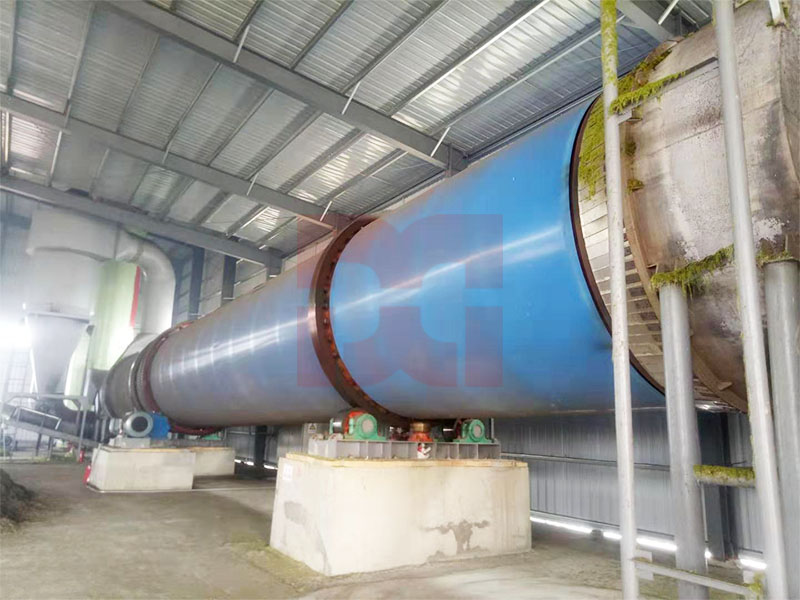
Biomass Rotary Dryer Parameters
Model | DDSG2006/3 | DDSG2008/3 | DDSG2010/3 | DDSG2212/3 | DDSG2510/3 | DDSG2512/3 | DDSG2912/3 |
Evaporation area(m2) | 76.93 | 105.19 | 133.46 | 142.55 | 168.92 | 204.72 | 247.42 |
Capacity(t/d) | 97.8-47.5 | 122.4-55.6 | 144.5-63.5 | 154.0-67.5 | 193.0-83.5 | 227.0-100.0 | 268.0-120.0 |
Evaporation capacity(t/h) | 1.066 | 1.200 | 1.850 | 1.976 | 2.427 | 2.912 | 3.432 |
Initial moisture(%) | 35-50% | ||||||
Final moisture(%) | 12-15%(can be adjusted) | ||||||
Drying temperature(℃) | 270±30℃(average temperature) | ||||||
Total power(kw) | 28-35 | 45-66 | 56-78 | 65-85 | 75-110 | 90-125 | 110-135 |
The plant total weight(kg) | 19500 | 22000 | 25000 | 27000 | 35000 | 38000 | 43500 |
Covering area(m2) | 8m*12m | 8m*15m | 8m*18m | 8m*18m | 10m*18m | 10m*20m | 10m*22m |
Application and After-Sales Service
Biomass Dryer Application
A biomass dryer is special equipment for drying various kinds of biomass.
Such as wood chips, sawdust, wood shaving, bark, alfalfa, bagasse, spent grain, kinds of poultry manure, etc.
Our After-sales Service
(1) Assign special constructors to go to the site for installation and commissioning.
(2) Training operators on site.
After installing the complete equipment, 1-2 full-time technicians will be left to assist customers in on-site production until the customers are satisfied
(3)After installing the complete equipment, 1-2 full-time technicians will be left to assist customers in on-site production until the customers are satisfied.