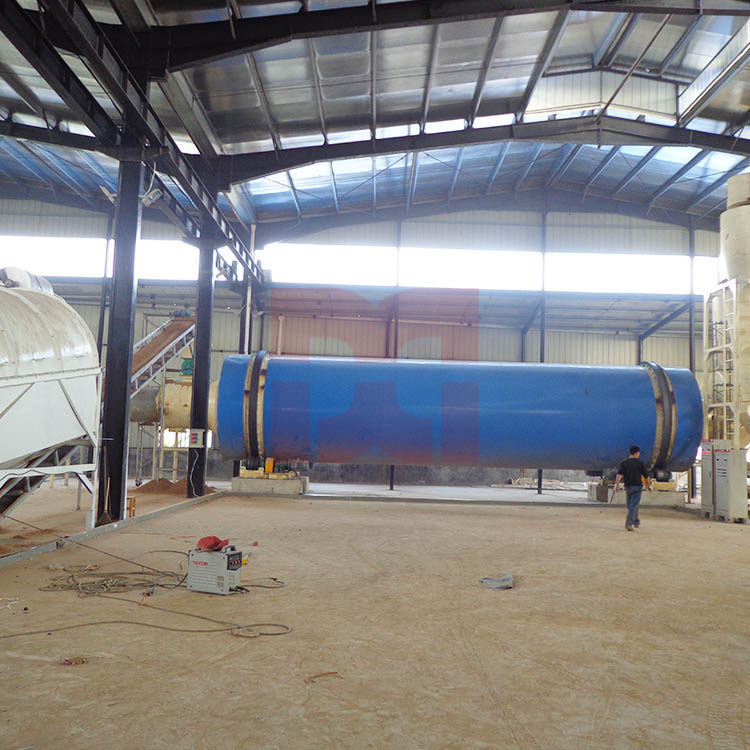
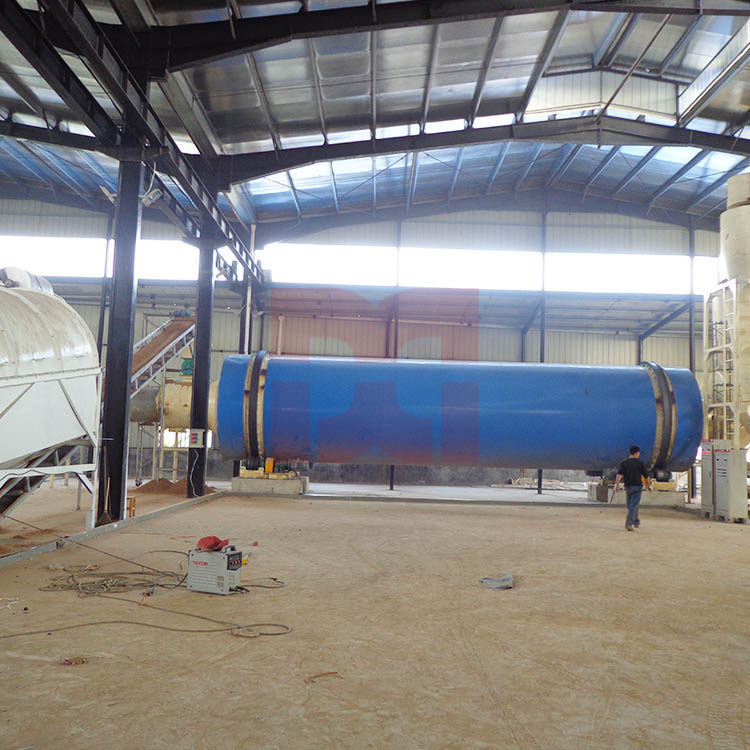
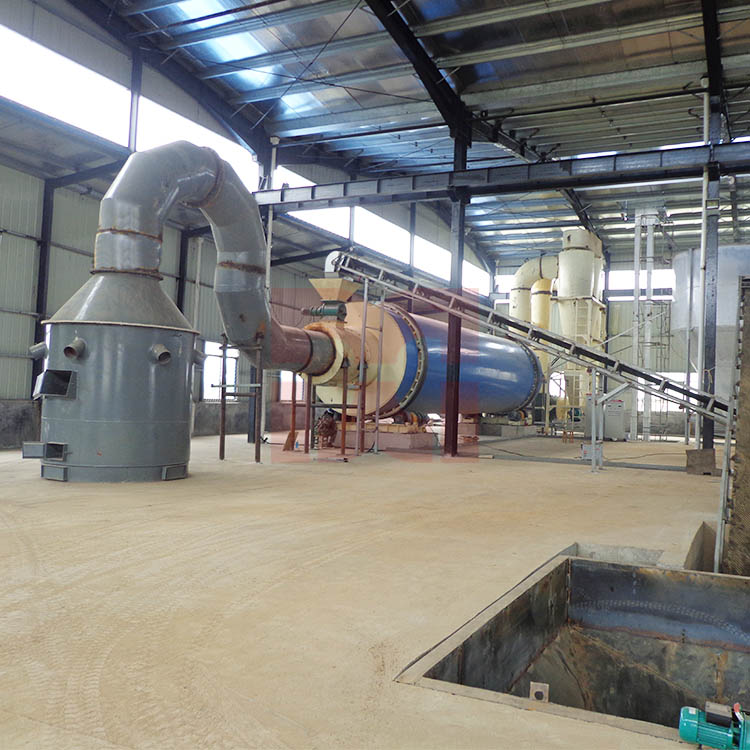
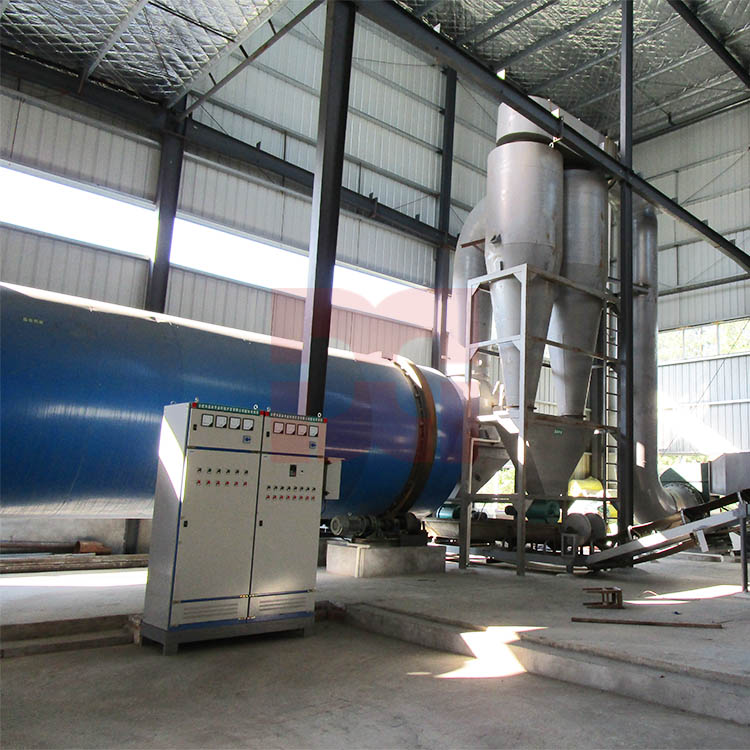
Sawdust dryer is specially designed and manufactured for drying sawdust, wood shavings, wood powder, wood chips and other materials. The large three-layer sawdust drum dryer is dehydration equipment developed by Zhengzhou Dongding for biomass pellet making of sawdust, wood powder and shaving materials , which can effectively improve the quality and appearance of final particles, The system effectively prolongs the drying time of materials and increases the air volume. It has the advantages of energy-saving, environmental protection, high efficiency and reduced floor space.
Sawdust Dryer Working Principle
Material enters the inner layer of the rotary drum by the feeder to realize downstream drying. Material is continuously picked up and scattered under the inner lifting board to realize heat exchange in a spiral manner. The material moves to the other end of the inner layer and enters the middle layer for countercurrent drying. Material is continuously raised in the middle layer and moves forward. The material in the middle layer fully absorbs the heat not only from the inner drum but also from the middle drum, at the same time prolongs the drying time, where the material reaches the expected drying state. The material travels to the other end of the middle layer and falls into the outer layer. The material travels in a rectangular multi-loop manner in the outer drum. The material that achieves the drying The effect is quickly discharged from the drum under the action of hot air.
Wet material failing to achieve the drying effect cannot move quickly because of its own weight. Material is fully dried in this rectangular lifting board, so as to achieve the purpose of drying.
Sawdust Dryer Features
1. Automatic stone removal and iron removal can ensure that the impurities do not enter the later process.
2. Using a hot air stove with a special flue design as the heat source, effectively avoiding a large amount of heat energy entering the drum and causing a fire in an emergency situation, and the operation is safer;
3. A new type of energy-saving hot air stove is provided, which is characterized by high efficiency, energy-saving, controllable thermal engineering, simple operation, reduced coal consumption by about 60%, high thermal insulation efficiency, low energy consumption and long service life.
4. Adopting a patented four-wheel drive device to ensure the stability and adjustability of the drying drum, while also protecting the safety of the driving motor;
5. The drum discharge system adopts a fully sealed design, which effectively prevents materials from being drawn away with the wind caused by air leakage, and at the same time prevents dust from flying;
6. Advanced dust removal and purification technology, high efficiency of the supporting dust collector, and low power consumption;
7. Adopting frequency conversion speed regulation to control the feed amount, and the final moisture index of the material can be controlled flexibly.
Sawdust Dryer Parameters
Model | DDSG2006/3 | DDSG2008/3 | DDSG2010/3 | DDSG2212/3 | DDSG2510/3 | DDSG2512/3 | DDSG2912/3 |
Evaporation area(m2) | 76.93 | 105.19 | 133.46 | 142.55 | 168.92 | 204.72 | 247.42 |
Capacity(t/d) | 97.8-47.5 | 122.4-55.6 | 144.5-63.5 | 154.0-67.5 | 193.0-83.5 | 227.0-100.0 | 268.0-120.0 |
Evaporation capacity(t/h) | 1.066 | 1.200 | 1.850 | 1.976 | 2.427 | 2.912 | 3.432 |
Initial moisture(%) | 35-50% | ||||||
Final moisture(%) | 12-15%(can be adjusted) | ||||||
Drying temperature(℃) | 270±30℃(average temperature) | ||||||
Total power(kw) | 28-35 | 45-66 | 56-78 | 65-85 | 75-110 | 90-125 | 110-135 |
The plant total weight(kg) | 19500 | 22000 | 25000 | 27000 | 35000 | 38000 | 43500 |
Covering area(m2) | 8m*12m | 8m*15m | 8m*18m | 8m*18m | 10m*18m | 10m*20m | 10m*22m |
Application and After-Sales Service
Sawdust Dryer Application
A sawdust dryer is a special equipment for drying various kinds of the wood fiber. Sawdust dryer is suitable for wood chips, wood shaving, wood power, bark, bamboo slices, alfalfa, kinds of straw, etc.
Our After-sales Service
(1) Assign special constructors to go to the site for installation and commissioning.
(2) Training operators on site.
(3)After installing the complete equipment, 1-2 full-time technicians will be left to assist customers in on-site production until the customers are satisfied.